INSIGHT: Deadly explosion at BASF’s Ludwigshafen site impacts major feedstock flows
Nigel Davis
19-Oct-2016
BASF’s steam
cracker II at Ludwigshafen lies at the heart of the company’s
verbund production strategy. Source: BASF
SE
By Nigel Davis
LONDON (ICIS)–The deadly explosion and fire at BASF’s Ludwigshafen site on Monday is having a major impact on the company with logistics flows for more than 20 plants at the site affected.
On Wednesday BASF had declared force majeure on propylene from the Miro refinery in Karlsruhe, Germany, FM on the ethylene pipeline sud and FM on naphtha to its own trading company in Switzerland, according a company source.
BASF says that many products are affected due to limited jetty availability at the harbour where the incident took place.
The accident claimed the lives of two of the company’s firefighters. BASF confirmed that another person was missing while eight were seriously injured with 17 others receiving light injuries.
The explosion occurred while firefighters were tackling a blaze in pipes carrying ethylene and propylene in the northern area of the giant chemicals site, the world’s largest.
Ludwigshafen’s two crackers were shut down and BASF confirmed on Tuesday that 20 downstream production units had shut.
BASF’s verbund business model sees to it that olefins and aromatics from the crackers are used downstream to make a range of commodity and speciality products.
The Ludwigshafen site is BASF’s most integrated. More than 200 production plants are located at the site connected by over 2,000km of pipelines and 200km of railway track according to data on the European Chemical Site Promotion Platform ECSPP). The site produces 8,500 products with a total volume of 8m tonnes/year.
A major disruption at the Ludwigshafen site, established in
1865, has the potential to have a significant impact on BASF.
The site spreads over 10 square kilometres on the banks of
the River Rhine. It is the most densely packed of the six
BASF verbund sites and the one where the verbund concept of
production integration was developed.
By comparison, BASF operates five other verbund sites – in
Antwerp, Belgium, Nanjing, China, Kuantan, Malaysia and at
Freeport and Geismar in the US. Only the Geismar site comes
anywhere close to Ludwigshafen in area – at 9.27 square
kilometres – but it accommodates only 23 production units.
The extent of the damage to pipelines and other infrastructure at the Ludwigshafen site is not known publicly, but the fact that the two crackers and a large number of downstream units are closed illustrates the potential impact of the fire and explosion on site integration.
There could well be workarounds that will enable units to re-start. And it may be possible to gauge the potential impact of the accident on on-going production when it is confirmed that the crackers are operating again.
A public update is expected from BASF on Wednesday afternoon or on Thursday. The company says on its Twitter feed that while it does not comment on individual plants it is “reaching out to those customers affected by the shutdowns”.
BASF runs its crackers in Europe to optimise olefins and aromatics production for the downstream businesses. The company says that the verbund concept was developed and optimised at Ludwigshafen before being applied around the world. The crackers form the heart of the facility, it adds.
The oldest was completed in 1965 and the second cracker added in 1980 with double the capacity. BASF says on its website that two million tonnes of naphtha a year are transported to Ludwigshafen by ship and pipeline. The crackers together producer about 620,000 tonnes/year of ethylene and 350,000 tonnes of propylene.
Steam crackers I and II mostly operate independently of each other, it adds, which allows for maintenance turnarounds.
ICIS data show that the crackers feed ethylene to downstream ethylene oxide and ethylbenzene production. There is some offtake from methyl methacrylate, linear low density polyethylene and various other ethylene derivative manufacture.
Propylene is used mainly to produce butyraldehyde (for plasticizer and other uses), acrylic acid and propylene oxide (PO), while butadiene is used largely for acrylonitrile butadiene styrene plastics production.
BASF uses benzene from the cracker for ethylbenzene and cyclohexane production.
Financial analysts are divided on the potential impact of the plant shutdowns. Markus Mayer of Baader Bank in Germany, commenting immediately after the accident, suggested that it could have a negative 1% to 3% impact on the group’s 2016 earnings before interest, tax, depreciation and amortisation (EBITDA). That initial analysis was based on the influence of an extended shutdown on the company’s chemicals segment.
About 6% of BASF’s annual EBITDA might be directly impacted by the fire, he added. “The shutdown might last more than a quarter, in our view. Therefore 1-3% of EBITDA might be at risk,” he told ICISnews.
Oliver Schwarz at Warburg research was more circumspect, suggesting that it was too early to assess the damage at Ludwigshafen. Workarounds for logistics are more easy to undertake than damage to production units, he stressed. The bank does not believe that the Ludwigshafen crackers will be offline for several weeks, let alone months.
Currently, the situation looks very much like a logistics issue as the explosion and fire took place on the harbour area where the site receives and ships bulk feedstocks and chemicals by river barges. The Ludwigshafen site can receive and deliver product by pipeline, ship, river barge, rail and truck.
Global News + ICIS Chemical Business (ICB)
See the full picture, with unlimited access to ICIS chemicals news across all markets and regions, plus ICB, the industry-leading magazine for the chemicals industry.
Contact us
Partnering with ICIS unlocks a vision of a future you can trust and achieve. We leverage our unrivalled network of industry experts to deliver a comprehensive market view based on independent and reliable data, insight and analytics.
Contact us to learn how we can support you as you transact today and plan for tomorrow.
READ MORE
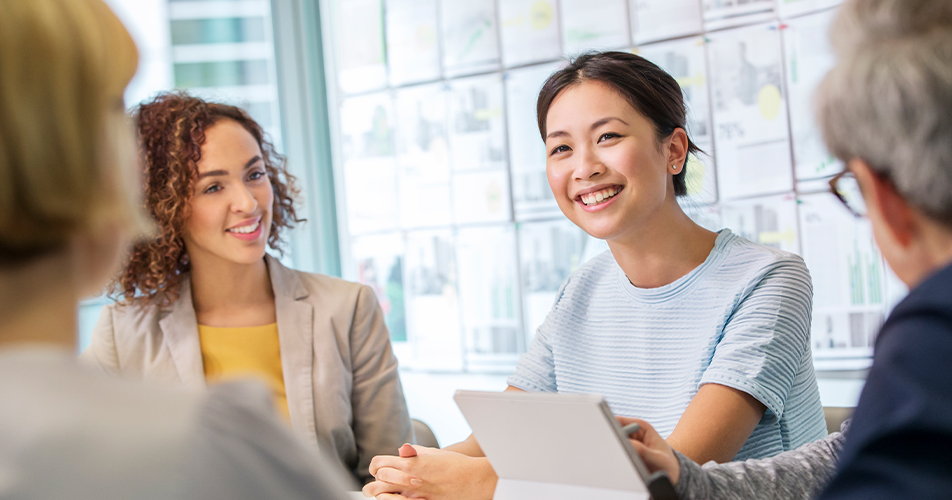