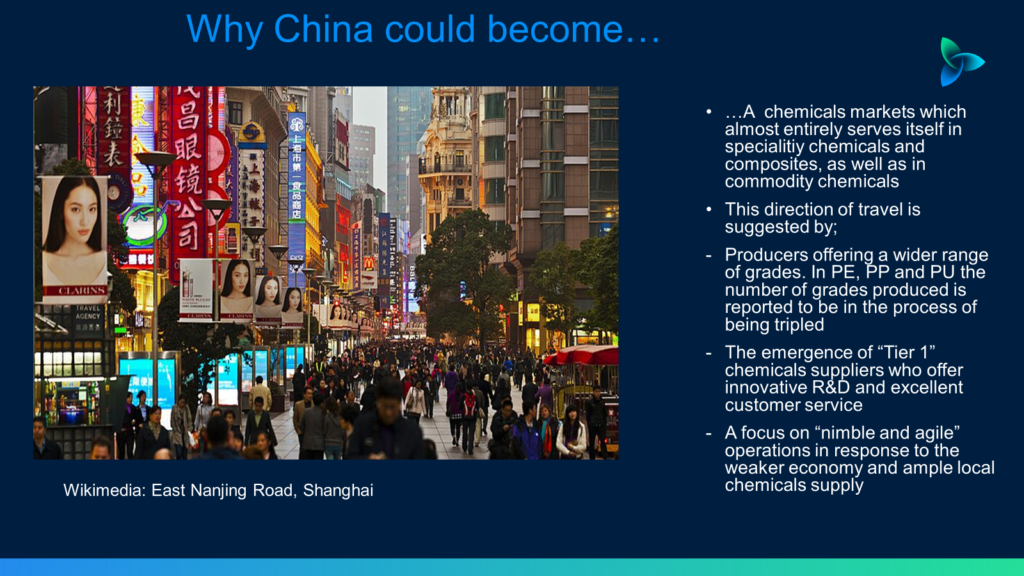
By John Richardson
AS RECENTLY AS three years ago, China’s chemicals producers would just about always run flat out regardless of the market conditions.
This was to “to keep people working in the washing-machine factory by making sure they never ran out of raw materials [polymers and composites]”, said the former chairman of one of the world’s biggest chemicals companies.
Chinese producers enjoyed some years of astoundingly strong profitability during the 1992-2021 Supercycle. But at times of poor earnings, plants still ran hard.
What’s changed since the Evergrande moment is weaker chemicals demand growth. The bursting of the property bubble has occurred as a lot more local supply has come on-stream, intensifying competition among local chemicals producers in many of the basic polymers.
The new emphasis, driven by the State-owned companies as always, was on being “nimble and agile”, said market sources.
This involved producing everything up and down the value chains only when it made economic sense and increasing the differentiation of grades for a broader range of more sophisticated applications, they added.
Better netbacks drive more local intermediate chemicals sales
A lot of this differentiation was aimed at supplying chemicals and polymers for higher-value downstream industries such as electric vehicles and batteries, they said.
There are said to be plenty of intermediate chemicals available locally that can compete with opportunistic imports. Local producers of intermediates are also reported to make better domestic netbacks than selling overseas.
Customers of local intermediate producers increasingly value reliable suppliers who can provide a wider range of grades, technical services and local currency deals, I’ve been told.
Add these factors together and “local-for-local” complete chemical supply chains appear to be more common.
The ability of chemicals importers to compete on price alone seems to be under challenge as a sustainable business model.
One industry source described his visit to to super-efficient very modern sites where the focus was on how China can make all the grades of chemicals and polymers it needed as it became a more developed economy.
This is said to apply to polyethylene (PE), polypropylene (PP) and polyurethane (PU) where local producers are reported to be tripling their range of grades as they broaden their licensing of technologies.
Tier I local suppliers will be among the winners
The source saw no reason why China wouldn’t meet all its own needs in PP quicker than was commonly assumed, including sufficient local output of high-impact, block- and random copolymer grades.
He saw the future winners in China as being what he called the Tier 1 suppliers. These suppliers would make all the grades necessary to serve ever-more sophisticated local end-use markets, which would require constantly successful R&D and good technical services, he said.
“These Tier 1 guys have highly skilled and knowledgeable sales and marketing executives with many years of experience, and who are loyal – they tend to remain with their employees for a long time,” added the source.
He contrasted this with Europe where he said that there was a lack of young people entering the industry and a lack of experience because of the image of “dirty old petrochemicals”, whereas in China the industry had a much more positive image.
A continued boom in specialities demand
Regular readers of the blog will be aware that I believe China has moved into an era of much lower GDP growth because of an rapidly ageing population, the collapse of the real-estate bubble and the geopolitical split with the West.
With lower GDP growth will come much-reduced annual percentage increases in demand for commodity chemicals. Increases will be in the low single digits compared with around double-digit growth rates during the 1992-2021 Supercycle.
But what has always been different about speciality chemicals and clever compounding solutions is that growth is much more divorced from GDP than in commodities.
As China’s economy continues to develop, albeit at a slower headline rate, speciality and compounding markets should continue to boom.
A lot of this strong growth will likely be driven by sustainability and cost efficiencies, as of course is the case with specialities and compounding everywhere.
Let’s use the building sector as an example. China wants 25% of new homes to be built by 2030 using modular materials. Achieving this target may involve innovations in compounding including the use of polymers.
Modular buildings in China are said take three months to build as opposed to the six months for conventional buildings, save on costs, and are more sustainable because the materials can be recycled.
Sure, China has a huge oversupply of housing in its richer provinces. But you cannot move housing across provincial borders to poorer provinces where the quality of housing is low.
A vast continent-sized markets serving itself
The next question on the exam paper as China’s chemicals industry becomes more and more sophisticated is this: Will China become a major exporter of speciality chemicals and composites?
Focusing on low-cost modular building materials, the challenges and therefore opportunities in the developing world are huge.
“Decent and affordable housing is in desperately short supply The UN estimates that 230m people in sub-Saharan Africa are living in what it defines as slum households; – roughly half the continent’s urban population,” wrote African Business in this July 2023 article.
China’s ability to export its lower-cost and perhaps sustainable housing solutions to alleviate Africa’s housing crisis seems unlikely to be constrained by geopolitics, as China is building closer relationships with the developing world as its split with the West widens.
It may, however, find it increasingly difficult to do chemicals business with the West where specialities markets are more sophisticated and so offer higher returns.
But while the outlook for China’s exports of speciality chemicals and composites seems uncertain, I believe we can conclude the following: China will become a vast continent-sized market that will largely serve itself.
I earlier discussed in detail how self-sufficiency is increasing in commodity chemicals, resulting in a pivot by “overseas-based” producers to specialities and composites.
China could become just about entirely self-sufficient in commodity grades of PP, PE and in paraxylene (PX) and ethylene glycols (EG) by 2030. The latter two chemicals are of course pure commodities.
Note the above phrase “overseas-based” rather than overseas, as the foreign investors in China are in strong positions to take advantage of this vast and rapidly maturing market.
For the reason just discussed, I don’t believe that the pivot by overseas-based producers to specialities and composites will work if it is based on exporting to China.
What should the overseas-based producers do? Pretty much forget China as an opportunity as they focus on the rest of the world.