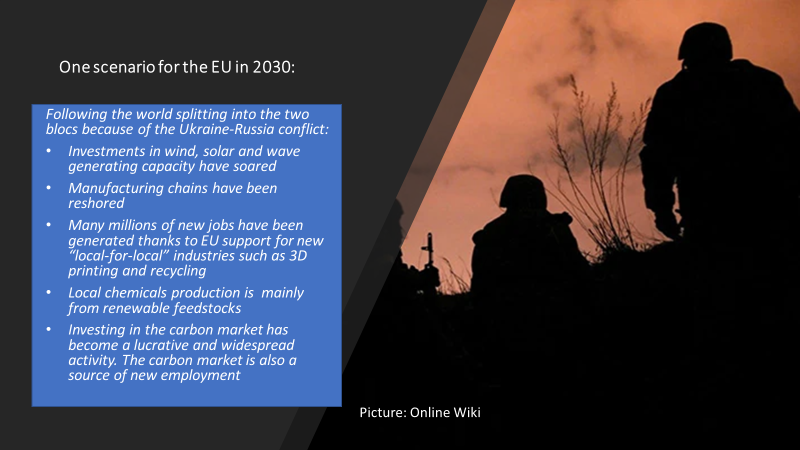
By John Richardson
MANY OF US HAVE only known a world of ever-more open borders and rapidly growing consumption of all the stuff made from petrochemicals and polymers.
But this world could now be disappearing because of the Ukraine-Russia conflict and growing pressure, at least on Western companies, to walk the talk on sustainability.
Two of the four megatrends – geopolitics and sustainability – may now be converging to entirely reshape the way that the petrochemicals industry works.
So, peering into my crystal ball, here is what our business world might look like in 2030. I focus only on the EU in this first post. I will look at other regions in later posts.
I must stress that this is only one scenario of many and none of us should believe for even one millisecond that we can predict all the outcomes. But I hope these thoughts help ICIS customers conduct the essential planning for what could be a very different future.
The EU economy in 2030
The world has split into two geopolitical and economic blocs – one led by the US and the other by China and Russia.
The Old Normal’s complex and simple (simple in that many relied almost entirely on China) global supply chains have been unwound and replaced by “local-for-local” manufacturing and service chains.
The energy shock immediately after the outbreak of the Ukraine-Russia crisis led to an “all hands-on-deck” approach in order to keep the EU economy running.
The number one short-term priority was reducing the EU’s dependence on Russian oil and gas – and, specifically for the petrochemicals industry, Russian naphtha. Around 50% of European naphtha was supplied by Russia before the crisis.
Old coal-run power plants were fired- up as LNG imports increased, supported by major investments in “floating regasification” facilities. These were converted LNG tankers that were quicker solutions than building regasification plants on land.
As the US and the EU moved economically and politically closer together, a lot of the extra LNG came from the US via its big shale gas reserves.
The EU recognised early in the crisis that if it were to become more energy independent, it would need to invest more in renewable energy because of its lack of hydrocarbon reserves.
Investors doubled down on pressure to make European companies decarbonise once. when the immediate energy crisis was over. This was driven by big increases in EU CO2 emissions as LNG was imported and as more coal was burned.
The EU stepped-up legislative pressure on companies to decarbonise, once the first phase of the Ukraine-Russia crisis was over.
Investments in wind, solar and wave generating capacity soared as breakthroughs were achieved in storing electricity in batteries. EU investment supported the development of more sophisticated batteries – the “Sparking Innovation” initiative.
The split with the China and Russia bloc led to a very painful period of economic adjustment.
The old “throwaway society” –- the one where Europeans would, for instance, buy clothes and throw them away before they were worn out – has disappeared for both economic and environmental reasons.
China had been the low-cost workshop for the West. But because of the new geopolitical divisions, manufacturing chains have been re-shored.
With labour costs much higher in the EU, new low-cost manufacturing methods had to be created to compensate for higher labour costs.
The higher labour costs could not be fully passed onto consumers, as between 2022 and 2025 the EU suffered from low economic growth and high inflation.
The key priority in those early days of the crisis was to avoid the stagflation of the 1970s: Low growth, high inflation and high unemployment. Many millions of new jobs have been generated thanks to EU support for new local-for-local industries such as 3D printing.
It is remarkable to think, how, before the crisis, we threw away so many computers, washing machines and dishwashers because repairs were more expensive than buying new devices.
Small-scale 3D printing workshops operate across the EU that print low-cost spare parts and some finished products.
The growth of renewable energy and 3D printing has lowered carbon emissions – and has generated vast amounts of new wealth through the extended carbon credits scheme.
Investing in the carbon market has become a lucrative activity for private investors, institutional investors and manufacturing companies. Lots of new employment has also been created in carbon markets.
What the EU chemicals industry looks like
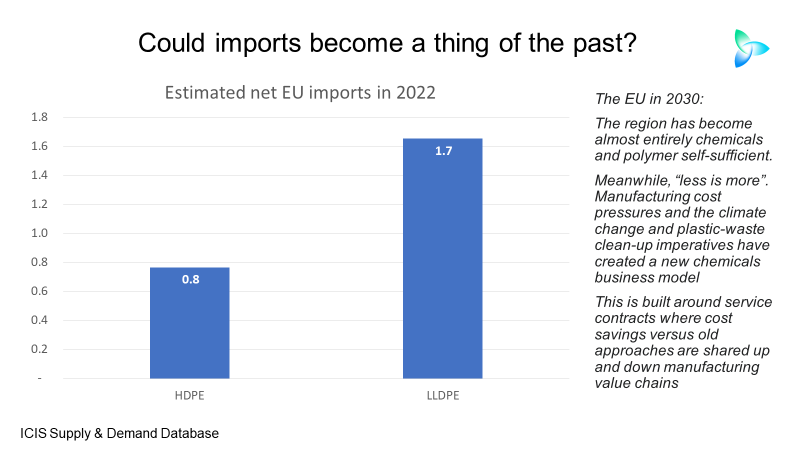
Immediately after the crisis began, the European petrochemicals industry saw big operating cuts because of oil and naphtha shortages and power cuts.
But in major polymers such as polyethylene (PE) and polypropylene (PP), there was plenty of global supply around because of a global recession coinciding with large amounts of new capacity.
Producers that had operations in the Middle East and US prospered, as well as in the EU, were able to import low-cost resins from other plants.
But the EU-only producers lost sales volumes and market share as they cut production. High oil and naphtha prices also ate into their margins.
The EU recognised the pain. But the short-term priority was securing enough resins to maintain essential food and medical supply chains.
When this initial phase of the crisis was over, local petrochemical companies worked with the EU to localise production for cost, environmental and job-creation reasons.
As electrification of transportation further accelerated, if you can excuse the bad pun, the dependence on imported oil declined.
Refineries that were no longer needed were turned into “energy centres”. People stopped talking about petrochemicals and instead referred to chemicals.
Old refineries were converted to make bio-ethanol which then makes ethylene. Blue and green hydrogen investments took place – along with big investments in chemicals recycling.
The economic breakout of chemicals recycling –- the result of both public and private money –- was a classic case of “needs must”. The increased economic efficiency of the technologies led to hundreds of small chemicals recycling plants next to landfills.
The output is collected and sent to centralised upgrading units. These units convert pyrolysis oil into the right quality for the steam crackers and reformers that continue to operate.
The EU has become almost entirely chemicals and polymers self-sufficient thanks to these investments and a carbon border adjustment mechanism that limits imports from less carbon-efficient countries.
Meanwhile, “less is more”. Manufacturing cost pressures and the climate change and plastic -waste clean-up imperatives have created a new chemicals business model.
No longer is financial success driven by sales-volume growth in chemicals. The measure of success is instead the efficiency of long-term service contracts with chemicals end-users.
Let me give you just one example of how this works, from the car-tyre manufacturing and hire-car fleet industries.
Pyrolysis oil from chemicals recycling plants is the main feedstock for an EU company’s crackers and reformers.
Carbon produced by the company’s steam crackers and reformers that make mixed C4s, ethylene, benzene and styrene is captured and stored. So is the carbon from downstream butadiene extraction and styrene plants.
Carbon is also captured from styrene butadiene rubber (SBR), butadiene rubber (BR) production and from making car tyres.
All the upstream companies in this value chain work together to offer a service package to a car-hire company. The package lasts ten 10 years and is built on “old business model” costs versus the new model that involves minimising the need for new tyres.
Largely autonomous-driven vehicles are programmed to drive in ways that reduce wear-and-tear on tyres.
Customers who prefer to drive vehicles are educated in driving techniques that reduce wear-and-tear. Tachograph readings are taken at the end of each car hire, with customers who drive smoothly receiving discounts of hire fees or lower insurance premiums.
Worn- out tyres are re-treaded at a local 3D printing workshops, using new speciality grades of SBR and developed by the synthetic rubber producers. The new grades maximise tread life.
These same resins are used for the new tyres that still need to be manufactured. Cost savings versus the old business model are shared across the whole value chain.
Every EU manufacturer is under pressure to better manage their Scope 3 emissions. These are the “emissions which are the result of activities from assets not owned or controlled by the reporting organisation, but that the organisations indirectly impacts in its value chain,” according to the US Environmental Protection Agency.
The players in this manufacturing chain share their expertise on Scope 3 emissions management – and the carbon credits that accrue from this expertise.
Conclusion: operational chaos must not get in the way of long-term planning
I’ve never known market conditions as volatile and as muddled as this. So, of course, operating teams are focusing very heavily on trying to interpret every scrap of data and market intelligence to forecast what might happen next.
But you cannot allow market chaos to suck the energy out of long-term planning for scenarios such as the one above.
If you do allow this to happen, you could end up with a business model that no longer works. This may happen quicker than you imagine because of the collision between geopolitics and sustainability.