A guide to major chemical disasters worldwide
Andy Brice
02-Oct-2008
Disaster is a rarity in the chemical industry, but negligence or misfortune can so easily result in devastating consequences
CONSIDERING THE potentially dangerous materials and processes employed in the chemical sector, most producers can be justifiably proud of their health and safety records. Occasionally, however, things do go wrong.
Aside from the immediate implications surrounding a major incident, such as loss of life, a threat to the environment or the destruction of plants and surrounding buildings, the damage to the industry’s reputation is almost irrevocable.
“If you measure the fears of the population about chemicals all over Europe, then air pollution, water pollution and the risk of plant catastrophes are still the most important to them,” says Daniel Verbist, executive director responsible for communications at the European Chemical Industry council (Cefic).
But from each disaster, lessons can be learned, he says – and these can often lead to the introduction of more stringent health, safety and environment legislation.
“The Seveso disaster [in Italy] in 1976 was a major environmental incident and the trigger that made people realize that a Europe-wide environment policy was needed it marked the birth of the [Seveso] directive,” says Verbist.
“But without doubt, Bhopal [in India] in 1984 was the most important catastrophe ever seen in the chemical industry,” he says. “At that time, the chemical industry was already preparing the Responsible Care initiative, but Bhopal triggered its launch the following year.
Responsible Care remains a major global initiative specific to the chemical industry that helps to improve performance in safety, health and environmental protection. The program was extended in 2006 to focus on new and important challenges, including product stewardship and dialogue over sustainable development.”
Similarly, events such as those at Flixborough, in the UK, Texas City in the US and Toulouse in France, have led to plenty of soul-searching and a reassessment of procedures. Rules and regulations are constantly being reappraised to prevent similar incidents.
Here is a selection of some of the industry’s worst moments.
OPPAU, GERMANY – September 21, 1921
Workers at BASF’s Oppau site, in Germany, decided that the best course of action to loosen a 4,500 tonne mound of ammonium nitrate (AN) and ammonium sulfate that had solidified was to detonate several dynamite charges.
Unfortunately, the use of this tried-and-true method was not suited to the explosive nature of AN, resulting in a massive 125m (410ft)-long and 19m-deep crater and the deaths of more than 500 people.
The accident destroyed around 80% of the homes in Oppau and ripped the roofs off houses as far as 25km (10 miles) away.
AN has since been responsible for numerous explosions in the chemical sector globally, as well as many acts of terrorism. Strict measures have been imposed to ensure the safe handling and storage of the fertilizer.
TEXAS CITY, TEXAS, US – April 16, 1947
On the morning of April 16, 1947, a French ship – The Grandcamp – was being loaded with ammonium nitrate (AN) fertilizer. With over 2,000 tonnes of AN onboard, a fire started in the hold. Not wanting to damage the cargo, the captain refused to use water on the flames and opted instead to control the fire using the steam system.
The heat intensified and the ship exploded, killing crewmembers and showering onlookers with shrapnel. The blast was heard over 150 miles (240km) away.
A 15ft (4.6m) wave swept a barge ashore, buildings were destroyed – including a Monsanto chemical plant nearby – and the ship’s anchor was found more than a mile away. There were around 3,500 injuries and 576 people were killed.
TEXAS CITY, TEXAS, US – March 23, 2005
The 2005 disaster at UK oil major BP’s Texas City refinery, in Texas, US, was considered the nation’s worst industrial disaster in 15 years.
A series of explosions occurred when a hydrocarbon isomerization unit was restarted and a distillation tower flooded with hydrocarbons. As a result, 15 were killed and another 180 were injured. BP admitted to charges and accepted fines last year, with BP America chairman Bob Malone conceding that the company was guilty of a felony “for failing to have adequate written procedures for maintaining the ongoing mechanical integrity of process equipment at the Texas City refinery.
“If our approach to process safety and risk management had been more disciplined and comprehensive, this tragedy could have been prevented,” he said.
JILIN CITY, CHINA – November 13, 2005
A series of explosions rocked China-based Jilin Petrochemical’s 70,000 tonne/year aniline complex in Northeast China, killing five and injuring 70. Benzene also leaked into the Songhua river and caused millions of people to go without drinking water, with many fleeing their homes.
Initial investigations suggested the explosion occurred after operators attempted to unblock a nitrobenzene rectification tower. Jilin’s Bureau of Production Safety Supervision and Administration concluded that a valve was left open, causing temperatures to rise rapidly.
Nearby equipment and storage tanks containing nitrobenzene, benzene and nitric acid feedstocks also caught fire and exploded. Water and electricity supplies had to be cut off as local residents reported tap water turning red or yellow. There were also concerns that water supplies to some Russian towns could be affected by the contamination of the river.
BHOPAL, INDIA – December 3, 1984
A gas leak at US-based Union Carbide’s pesticide plant in Bhopal, India, is cited as one of the chemical industry’s greatest tragedies.
On December 3, 1984, methyl isocyanate gas leaked from the facility during the early hours of the morning while local residents slept. Around 2,000 people died immediately, with another 8,000 dying later.
The initial investigation suggested that large volumes of water had entered the chemical tank, which caused a chemical reaction and led to the leak. The incident highlighted the problem of urbanization and having a plant located near a densely populated area. In 2001, Union Carbide became a wholly owned subsidiary of US giant Dow Chemical.
FLIXBOROUGH, UK – June 1, 1974
In 1974, cyclohexane vapor leaked from ruptured pipework at the Nypro (UK) site at Flixborough. This resulted in an explosion that killed 28 people and injured 36.
Offsite, 53 injuries were reported. Property in the surrounding area was also severely damaged.
The disaster led to the Health and Safety at Work Act, introduced the same year, when the Health and Safety Executive was also established.
On July 10, 1976, in a small Italian town north of Milan, a reactor at the ICMESA chemical plant overheated, resulting in an explosion and the first, and highest known exposure, to dioxins in a residential area. A toxic cloud containing 2,4,5-Trichlorophenol – used to make pesticides and antiseptics – spread to the densely populated city of Seveso.
This became the catalyst for the Seveso Directive, in 1982, which has since undergone numerous amendments. It was replaced by the Seveso II directive in 1996.
TOULOUSE, FRANCE – September 21, 2001
Some seven years later, there is still no official ruling on the cause of the 2001explosion at Atofina’s Grande Paroisse fertilizer plant in Toulouse, France. A report is now expected toward the end of this year or the beginning of 2009.
Around 300 tonnes of ammonium nitrate (AN) exploded, destroying the site and wrecking buildings 3km (1 mile) away in the city center.
The blast left a crater 50m (164 feet) wide and 10m deep. It was responsible for the death of 30 people, and 10,000 injuries.
SCHWEIZERHALLE, SWITZERLAND – November 1, 1986
Water used to extinguish a major fire at the Sandoz chemical factory in 1986 washed chemicals into the river Rhine, one of Europe’s busiest waterways. The spill caused severe pollution, which took years to eradicate, and killed an estimated 500,000 fish.
The incident highlighted the need for antipollution legislation in Europe. Soil was excavated from the area and decontaminated to ensure there was no risk to the groundwater.
The German chemical company also developed a new framework for warehouse safety, including segregated storage for different risk categories of chemicals, and fire measures such as retention basins for run-off water.
Take a look at a timeline of global chemical disasters
Global News + ICIS Chemical Business (ICB)
See the full picture, with unlimited access to ICIS chemicals news across all markets and regions, plus ICB, the industry-leading magazine for the chemicals industry.
Contact us
Partnering with ICIS unlocks a vision of a future you can trust and achieve. We leverage our unrivalled network of industry experts to deliver a comprehensive market view based on independent and reliable data, insight and analytics.
Contact us to learn how we can support you as you transact today and plan for tomorrow.
READ MORE
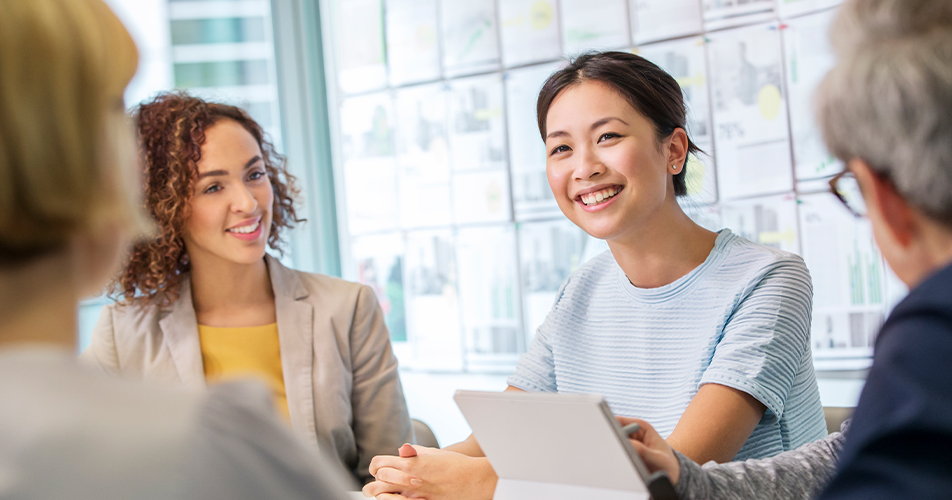