Polymer manufacturers develop novel solutions for the auto industry
Elaine Burridge
21-Apr-2010
Carmakers are turning to polymer manufacturers to develop breakthrough solutions addressing the key drivers of reducing weight and cost
Innovative plastics and composites are making inroads in automotive applications where metal has traditionally been used.
The trend to replace metal is opening up a myriad of opportunities for polymer manufacturers, as it also allows designers to integrate functionality that may not have been possible with metal versions.
Products are being developed for under-the-hood (UTH) applications that can withstand a hot and chemically aggressive environment, as well as for structural parts.
There are fenders with online paintability, as well as a new generation polymers that have high heat and chemical resistance over longer periods of time. US chemical giant DuPont has a new family of polyamide grades for UTH applications.
France’s Rhodia has a range of polyamides with long-term barrier resistance and is also developing a breakthrough thermoplastic-based material that it expects to present at Germany’s K trade fair in October.
Polycarbonate (PC) use in front windshields remains a development focus. SABIC Innovative Plastics of the US has a plasma coating for PC that improves scratch resistance and helps to address industry concerns regarding resistance to wiper abrasion.
Stephen Shuler, chief technology officer of SABIC Innovative Plastics’ wholly owned subsidiary Exatec says that it has expanded its team in Bangalore, India, to study how abrasion occurs.
Shuler says PC has big advantages in terms of styling and aerodynamic qualities, as well as saving weight. “There is a big opportunity in back lights, side windows, and roofs, which have seen a lot of activity.”
Green materials are another focus. DuPont says that several automotive original equipment manufacturers (OEMs) aim to incorporate biopolymers and, in some cases, specific eco-friendly car lines will be developed. It predicts that biopolymers’ share in automotive will steadily rise, but will still remain low in the short term, compared with petroleum-based polymers.
SABIC Innovative Plastics has introduced polybutylene terephthalate (PBT) iQ grades derived from 85% post-consumer polyethylene terephthalate (PET) through a novel technology that upcycles solid waste. Venkatakrish Umamaheswaran, director of marketing, engineering and technology, automotive, says this is very popular as it allows carmakers to reduce their carbon footprint.
Rhodia has developed two ranges, based on bio-sourced and recycled materials. Last year, it launched a polyamide based on polyamide 610, partially made from castor oil. Innovation marketing manager Antoine Guiu says Technyl eXten is a high-performing polyamide with similar characteristics to polyamide 12 and is positioned for applications where polyamide is already well installed but where car companies are seeking greener options. It has also relaunched its recycled plastic, Technyl R.
While no one can say whether the all-plastic car will become a reality, Germany’s BASF estimates that 25% of the weight of a combustion-engine car could consist of plastics in 10 years, compared with 14-18% in the average European car now.
1. UNDER THE HOOD
DuPont has developed
Zytel PLUS, a new family of polyamide products with
improved durability that can double the life of thermoplastic
components exposed to hot, chemically aggressive and humid
environments. Four products were launched last month with
more planned for 2010. Target applications include charge air
coolers, turbo air ducts, engine mounts, cylinder head
covers, oil pans, transmission parts and others.
2. INTERIOR
SABIC Innovative Plastics’
STAMAX long fiberglass polypropylene (PP) resin is
used in floor consoles and instrument panels and is said to
deliver 10-15% cost savings and 20% lower weight, as well as
enabling parts integration. It has a better surface finish
than short fiberglass products, allowing molding in color and
processability.
Production of these resins, only available until now in Europe, has begun in the US, serving both the North and South American markets and the company is also looking to expand into the Asia-Pacific region.
Its Lexan EXL PC, which has good impact resistance and improved chemical resistance to automotive fluids, is now being validated for steering wheels. It will be launched in Asia first, some time in 2010 or early 2011.
Innovative and colored solutions are being developed for interiors. This year, US-based Dow Automotive Systems has introduced in Europe advanced polyurethane (PU) foam technology for instrument panels and interior trim, giving significant weight reduction, improved airbag deployment properties and fast cycle times. The product is already used by several North American OEMs and will be introduced by a leading European OEM in the coming months.
The company is also collaborating with polyvinyl chloride (PVC) suppliers to develop PU foam solutions for instrument panels that will not discolor or develop skin cracks.
Germany’s Bayer MaterialScience can create light-colored, ultraviolet and scratch-resistant surfaces for interior parts via its DirectSkinning technology developed with compatriot components manufacturer fischer automotive systems. The company says that parts produced by this process require very little secondary finishing.
A decorative panel is now in series production for a dashboard part in Germany’s BMW 5 Gran Turismo range. The 1.4mm-thick panel covering, based on Bayflex LS PU, is produced in five colors, including ivory white, light beige and gray.
3. FRONT END/STRUCTURAL
Germany’s
LANXESS has invented a
hybrid plastic-metal composite technology for high-strength
structural parts such as front ends, pedal support bracket
and brake pedals. In its first use in the front end of the
new German-based Audi’s A8, a 1mm-thick organic
plastic sheet (a thermoplastic reinforced with continuous
fibers) is used alongside aluminum sheet in the lower beam.
SABIC Innovative Plastics offers solutions for fenders with its Noryl GTX, and Cycoloy resins. Noryl GTX polyphenylene ether resin, used in US-based Ford’s Kuga, was the first pedestrian-compliant plastic fender and also features an energy absorption component made with Xenoy PC/PBT resin.
Cycoloy high-modulus ductile (HMD) PC/acrylonitrile-butadiene-styrene (ABS) resin allows three components to be integrated into one part. SABIC Innovative Plastics says its use in US-based GM’s Cadillac CTS spoiler is the largest and most critical part to date using HMD, which reduces mass by up to 40%, and delivers high modulus and low coefficient of thermal expansion.
BASF’s Ultramid polyamide resin has been chosen for a fender stiffener on a fourth model for Germany’s Opel. It says that compared with one made of PP, the lower fender stiffener is about 50% lighter and narrower at its widest point, as well as nearly three times stiffer and energy-absorbing.
BASF is using polyamide in transmission beams where it has replaced aluminum in BMW’s 5 series Gran Turismo 550i. Ultramid polyamide and Elastollan PU are used for a crash-active engine cover with integrated air filter for the 7 series.
Rhodia is launching an online paintable polyamide for fenders as part of its Technyl line that can withstand temperatures of up to 210-215˚C (410-419˚F) and has high dimensional stability. Guiu estimates that this will save 50% of the weight and 15% of the cost of steel.
Rhodia has also created the first polyamide reinforcement beam for truck radiator grills using Technyl Star AFX.
As for structural parts, Dow’s new fast-curing epoxy composite systems, SYNEXA, can save up to 40% in weight versus steel and enable cycle times of 10 minutes or less.
Nigel Shields, application development leader, Dow Automotive Systems, says it is working on improving SYNEXA‘s curing speed to less than 5 minutes, with commercialization likely to be two to three years away.
Halogen-free, flexible, Noryl resin for wire coating from SABIC Innovative Plastics replaces PVC. It has a thinner coating and can reduce the wire bundle diameter by up to 27%, and the bundle area by up to 47%. Toyota and Nissan of Japan, GM, and Korea’s Hyundai use it.
4. FRONT LIGHTING
SABIC Innovative Plastic’s Lexan PC and Cycolac
ABS were used to make the first personalized, illuminated
sill plates, providing high-impact lighting using just one
light-emitting diode bulb instead of up to 30, cutting costs
by up to 50% versus standard designs.
New Lexan products include Lexan XHT, which has very good temperature resistance, while providing clarity and colorability. Applications will be in front headlamps, head lamp bezels, fog lamp lenses and inner lenses where temperatures are significantly higher.
5. REAR – FUEL TANK
Rhodia’s new range of polyamide compounds, Fuel’In
by Technyl, has been developed for long-term
contact with fuel. Fuel’In is based on one layer,
unlike other plastics in these applications that are
multilayered with high density polyethylene (HDPE) and
ethylene vinyl alcohol (EVOH). Also, Fuel’In is
completely recyclable. “Polyamide is more fluid and
processable than HDPE or multilayered solutions, saving cycle
time and, for a part like a fuel filler neck, up to 30% less
material is needed,” says Guiu.
6. TRUNK
Reinforced polyamide 6 is used
in the Audi A8‘s spare wheel recess. LANXESS says its
Durethan DP BKV 60 H2.0 EF, a highly filled polyamide
6 with 60% fiberglass, enables precise injection molding in a
single stage.
CAR AND CHEMICAL MAKERS NEED TO
SYNCHRONIZE
The automotive sector is a hugely
important market for many chemical producers. But there is
little in the way of strategic interaction between the two on
product development.
A recent study by Germany’s Roland Berger Strategy Consultants and the European Chemical Marketing and Strategy Association (ECMSA) concluded that greater cooperation and fusing of the value chains of the two industries would bring significant rewards.
Says Thorsten Ploss, chemical partner at Roland Berger: “The chemical industry does not see the strategic needs of the carmakers, and the carmakers are not aware of what the chemical industry can do. Many chemical companies say they just can’t talk to the carmakers, and have to interact instead with the Tier 1 and 2 automotive suppliers.”
And if there is interaction, adds Ploss, it is generally on a short-term, tactical level to improve current models and reduce costs, not at the longer-term strategic level on future model development.
The study, finalized by the end of 2009, sets out a four-stage improvement process by increasing cooperation over a few years. One-to-one dialogues with a short-term focus are anticipated as the first step, moving gradually to group relationships and strategic collaboration by the end.
To kick-start the process, the ECSMA will be holding a workshop this September, bringing together chemical producers, major carmakers and their suppliers.
Global News + ICIS Chemical Business (ICB)
See the full picture, with unlimited access to ICIS chemicals news across all markets and regions, plus ICB, the industry-leading magazine for the chemicals industry.
Contact us
Partnering with ICIS unlocks a vision of a future you can trust and achieve. We leverage our unrivalled network of industry experts to deliver a comprehensive market view based on independent and reliable data, insight and analytics.
Contact us to learn how we can support you as you transact today and plan for tomorrow.
READ MORE
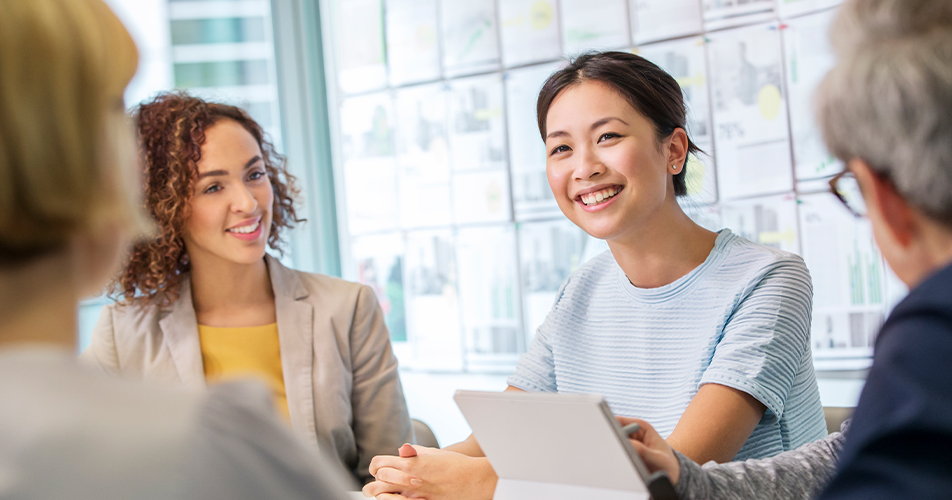