Desalination presents growing chemical opportunity
Cynthia Challener
22-Jul-2010
Correction: In the ICIS Chemical Business story titled “Desalination presents growing chemical opportunity,” Manel Soria was incorrectly identified as Manuel Soria. Additionally, GE Power &Water was incorrectly identified as GE Power & Water Process Technologies. A corrected story follows.
The growing desalination industry depends on a wide range of chemistries
MORE AND larger desalination plants came on stream in 2009 than in any previous year, bringing the global total to over 14,450, and driving the market for associated process chemicals to a new high.
|
---|
PHOTOLIBRARY |
These chemicals adjust pH, control scale, remove particulates, prevent biological fouling, clean and remineralize the highly purified product streams. Specialized chemistry is also required to synthesize the reverse osmosis (RO) membranes.
The overall desalination market is growing at about 10-15% on a global average, according to Paul Turgeon, president and chief operating officer of US-based BWA Water Additives Paul Turgeon. He estimates current worldwide consumption of chemicals used in both thermal and membrane desalination at $500m (€403m). Defining the consumption on a per-unit-water basis is nearly impossible, though, owing to the many factors that determine which chemicals are used and at what levels, such as the type and quality of the water source, the desalination method used and the severity of the conditions operated in.
Seawater desalination accounts for 62% of installed capacity as of June 2009, according to the US-based International Desalination Association (IDA). From 2007 to 2009, the installed capacity of seawater desalination plants expanded by nearly 30%. The largest plants are in the Middle East.
Of the two desalination methods, thermal processes account for 34% of installed capacity (mostly in the Middle East), while membrane processes account for just over 61%. Other technologies are electrodialysis (ED – 3.2%), hybrid technologies (0.7%), and electrode ionization (0.3%).
Thermal desalination, which essentially involves distillation of clean water from salts and other contaminants, is energy intensive, but relies on low-grade heat for much of the duty, reducing the energy cost, according to the IDA. RO membrane processes consume less energy, but use electricity, which is more expensive. The membranes are also expensive, but they generally last at least seven years. RO membranes are semipermeable. They allow water molecules under high pressure to pass through but repel salts and other dissolved and suspended particles.
TRENDS
Trends in the desalination
industry that directly impact chemical consumption include
reducing energy consumption, increasing operating
efficiencies and lowering costs, while also minimizing
environmental impact. “Specialty additives can be designed in
response to the composition of different water feeds, perform
at higher temperatures and lower pressures and under ever
higher salt concentrations. The overall effect is to increase
efficiencies, minimize waste and reduce cost,” says Turgeon.
Pretreatment chemicals used for brackish and seawater desalination include pH adjusters, coagulants and flocculants, deposit control agents (antiscalants, dispersants), biocides and reducing chemicals. In post-treatment, chemicals include chlorine, anti-corrosion additives and compounds for remineralization. Cleaning chemicals are also required.
Chemical treatments may be similar in thermal and membrane applications, but the technologies are adapted for each, says Manel Soria, product manager – membrane chemicals for GE Power & Water, of the US. “For membrane processes in particular, chemical additives are designed to restore and prolong membrane life, maintain system performance, reduce downtime and protect the membrane from oxidizing agents,” he adds.
In the case of some chemicals, changing technology has reduced demand. For example, to prevent scaling, the pH of feed water has traditionally been adjusted using hydrogen chloride or sulfuric acid. But it is becoming more common to replace acids with specialty antiscalants. The use of physico-chemical pretreatment with coagulants and flocculants (typically high-molecular-weight polyacrylamides) is also declining as pretreatment becomes more robust and the performance of equipment used to treat intake water improves, especially when combined with a set of organic coagulants.
Specialty antiscalants are based on organophosphonates and/or polyacrylates for membrane processes and anionic maleic polymers for thermal systems. These water-soluble compounds bind to impurities, preventing their deposition. Antifoaming agents (several classes of surfactants) are also necessary in thermal desalination processes. Additive suppliers such as BWA, GE and Netherlands-based Thermphos – Dequest provide specialized software packages that enable customers to select the most effective antiscalant chemistries and appropriate dosage levels based on the system’s specific operating conditions.
“New antiscalant technologies are being developed to allow use of new sources of feed water with different impurity profiles. They also ensure higher recovery rates of more concentrated brine streams, which have a higher tendency to scale. Thus it is critical to use proper antiscalants to avoid problems,” says Mark Eyers, global marketing manager for Thermphos – Dequest. To meet increasingly stringent brine discharge limits, Thermphos – Dequest works with new polymer and phosphonate chemistries to develop more sustainable/biodegradable antiscalants that provide the required performance profile but do not cause biofouling on membranes.
Antiscalants for thermal processes need to perform at ever higher temperatures. “Operating efficiencies in these plants improve at higher temperatures, and thus antiscalants need to continue to work effectively under such severe conditions,” explains Turgeon. BWA’s new Belgard EV2000 series products with a modified maleic backbone, end groups and side chains, as well as a narrower molecular weight distribution are designed to meet this growing need in the thermal desalination segment.
Biocides are also critical. They prevent biofouling, which is a major issue for membrane processes. Choices are limited, particularly because of compatibility issues with membrane chemistries and the need to meet regulatory requirements for potable water streams. Oxidizing biocides such as chlorine dioxide, as well as some organic, nonoxidizing compounds, are common. Even with these treatments, cleaning of desalination plants, typically with caustic soda and citric acid washes, is required on a regular basis.
The water that leaves desalination plants is often of very high purity and thus may need to undergo remineralization to reduce its aggressiveness. This process, according to Merv Ogston, Tech Solutions Engineer for Water & Wastewater at BOC Australia (part of Germany gases and engineering company Linde), involves injection of carbon dioxide (CO₂) and calcium hydroxide to form calcium carbonate. Chlorination and fluoridation typically follow as well. A new RO plant commissioned recently in Sydney, Australia, has a maximum design capacity of approximately 16 tonnes/day of CO₂.
“This technology for buffering desalinated water is the most cost-effective and efficient method available today,” says Ogston. “There is tremendous activity in the Asia-Pacific region, with many plants already in operation, under construction or in the planning stages, providing a tremendous growth opportunity for CO₂.”
Membrane manufacturers are also clearly benefiting from the strong growth in desalination. Membranes today are based on thin-film composite polyamide chemistry, which has replaced older cellulose acetate technology. These composites often include polyester, polysulfone, polyethersulfone or polyacrylonitrile layers, in conjunction with the top polyamide surface. Leading suppliers Dow Water & Process Solutions and Hydranautics, both US, continue to refine the chemistry to improve the salt and solid rejection rates at lower pressures and energy consumption levels, while reducing fouling and extending the lifetime of the membranes.
“Membrane chemistries are fairly similar, but some are designed to operate at lower pressures or to provide the highest separation,” says Richard Franks, manager of applications at Hydranautics. “The technology is in fact approaching the limits of energy savings due to the osmotic pressure of the salt solutions.”
ONGOING RESEARCH
Several groups are
researching alternative membrane technologies. Dow is
sponsoring research in the US at Virginia Polytechnic
Institute and the University of Texas at Austin targeting
development of oxidation-resistant RO membranes. Scientists
at University of California, Los Angeles, treated a polyamide
thin-film RO membrane with plasma to create active sites to
which were grafted polymer chains, forming a charged “brush
layer” that prevents fouling.
At Massachusetts Institute of Technology, researchers have developed a microfluidic device using ion concentration polarization that has the potential for use in portable desalination units. Seawater flows through microchannels connected by a Nafion (sulfonated tetrafluoroethylene-based fluoropolymer-copolymer) membrane. With an electrical field across the membrane, electrostatic forces repel salts contained in the seawater. The salts never pass through the membrane and thus fouling is avoided.
At the University of Western Australia, carbon nanotubes incorporated into membranes allow water but not salts to flow through at pressures much lower than those required for conventional RO membranes.
Meanwhile, researchers at the US’s Yale University are investigating forward osmosis technology, which uses the osmotic pressure of CO2 and ammonia dissolved in water on one side of the membrane to draw water through and leave salts behind. The CO2 and ammonia are driven off by heating and recycled, leaving pure water behind.
Global News + ICIS Chemical Business (ICB)
See the full picture, with unlimited access to ICIS chemicals news across all markets and regions, plus ICB, the industry-leading magazine for the chemicals industry.
Contact us
Partnering with ICIS unlocks a vision of a future you can trust and achieve. We leverage our unrivalled network of industry experts to deliver a comprehensive market view based on independent and reliable data, insight and analytics.
Contact us to learn how we can support you as you transact today and plan for tomorrow.
READ MORE
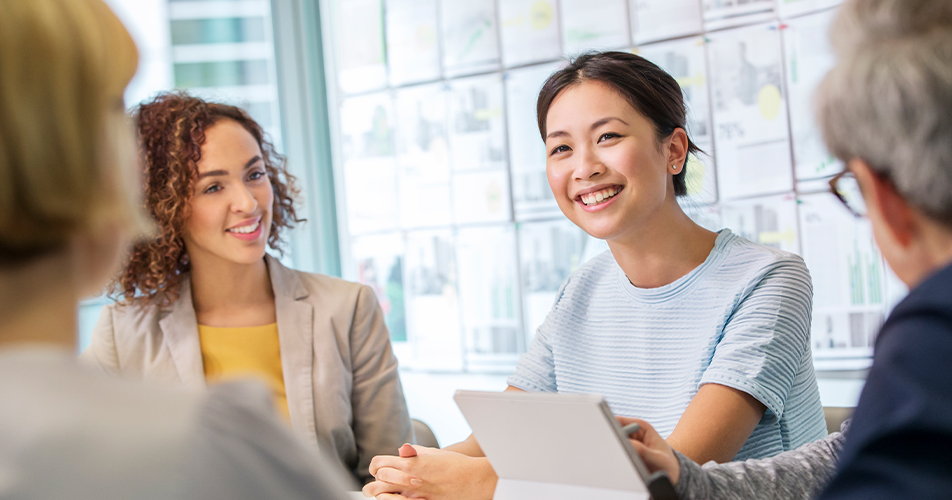