Innovation Awards: Polymers put CO2 to use
Mark Whitfield
16-Oct-2011
|
---|
|
Flexible polyurethane foam (top) and coatings are two products made from waste CO2 |
Catalyst technology to capture and reuse carbon dioxide in polyols and polymers has won Novomer the award for Innovation with Best Environmental Benefit
Waltham, Massachusetts, US-based sustainable polymer specialist Novomer has developed a technology platform that produces valuable, high-performance polymers from waste carbon dioxide. Novomer’s process is based on an innovative catalyst system that uses CO2 as a primary raw material in the production of polypropylene and polyethylene carbonates that contain between 43 and 50% CO2 by weight.
The polymers are based on the co-polymerization of CO2 and propylene oxide (PO) or other epoxides and can be produced as both thermoplastic polymers and polyols for packaging and coating products. The firm also has developed chain transfer technology to produce low molecular weight CO2-based polyols for thermoset applications that are commercially viable in coatings, adhesives, foams and composite resins.
The original catalyst development was carried out at Cornell University by Professor Geoff Coates and Scott Allen, now chief scientific officer and vice president of catalyst development, respectively, at Novomer and co-founders of the company. According to Peter Shepard, Novomer executive vice president, polymers, “before CO2 was even seen as a greenhouse gas, Geoff Coates had the novel idea of using it in a useful way as a low-cost raw material to make commercially viable products.”
Efforts, as early as 1970, to produce polymers from CO2 had not been commercially successful as the zinc-based catalysts used were not sufficiently reactive and created polymers with imperfect backbones. Novomer’s cobalt-based catalyst overcomes these problems and is over 25 times more active than earlier catalysts, producing a precise CO2-epoxide molecular structure that maximizes CO2 incorporation and improves polymer performance. Over the past two years, Novomer has achieved a 300-fold improvement in activity achieved over the earlier catalysts.
The polyols are produced in a batch process in units of 250 gal (946 liters) and a continuous process is being developed. According to Shepard, “the batch process is suited to producing smaller volumes of specialty products, while a continuous process will be used for producing larger volumes of single product.”
Novomer says that compared to traditional plastics, its CO2-based polymers are more environmentally friendly, and have mechanical and barrier properties that perform well for a variety of flexible and rigid packaging applications.
In addition, they are well-suited as resins for protective and decorative surface finishes for metal, wood and plastic. Novomer has developed partnerships to exploit its technology in new markets. In 2010, it entered an agreement with Netherlands-based DSM jointly to develop the production of coating resins using the technology. The resins produced are used in a number of applications including can and coil coatings, the automotive industry, printing inks and maintenance.
“DSM brings with it extensive applications experience. As the technology addresses a number of markets it is much quicker and efficient to partner with a company like DSM when developing new applications,” Shepard says.
SUSTAINABLE PRODUCT
Over the past 18
months, the firms have tailored the molecular structure and
functionality of the polyols for coatings and have produced
CO2-based coating resins that are both sustainable and have
equivalent or superior performance as traditional,
petroleum-based coatings in terms of flexibility, hardness,
environmental resistance and processing characteristics.
Backed by $18.4m (€13.5m) of funding from the US Department of Energy, Novomer is working with Albemarle and Eastman Kodak on phase two of the $106m US Recovery Act investment aimed at reducing CO2 emissions. Novomer is one of only six companies selected from 12 to move into pilot scale development. The project aims to achieve a continuous process for the production of commercially ready polycarbonate packaging products including bottles, coatings on beverage cans and other wood and metal surface applications.
During the two-year, $23m project, Novomer will work to scale up its products with Albemarle at its Baton Rouge, Louisiana, and Orangeburg, South Carolina, facilities and with Eastman Kodak at its Rochester, New York, location. Praxair is also a partner in the project and supplies the waste CO2.
Looking forward, Shepard says, “displacement of petroleum and the sequestration of CO2 in the final product are key benefits. Ideally, we see this as an integrated process where pressurized waste CO2 could be piped directly into our process – the manufacture of ethylene oxide (EO), ethanol, ammonia and hydrogen, for example, all produce the right quality CO2 as a waste stream.”
For more information on Novomer and its innovative carbon-capture technology, go to www.novomer.com
Global News + ICIS Chemical Business (ICB)
See the full picture, with unlimited access to ICIS chemicals news across all markets and regions, plus ICB, the industry-leading magazine for the chemicals industry.
Contact us
Partnering with ICIS unlocks a vision of a future you can trust and achieve. We leverage our unrivalled network of industry experts to deliver a comprehensive market view based on independent and reliable data, insight and analytics.
Contact us to learn how we can support you as you transact today and plan for tomorrow.
READ MORE
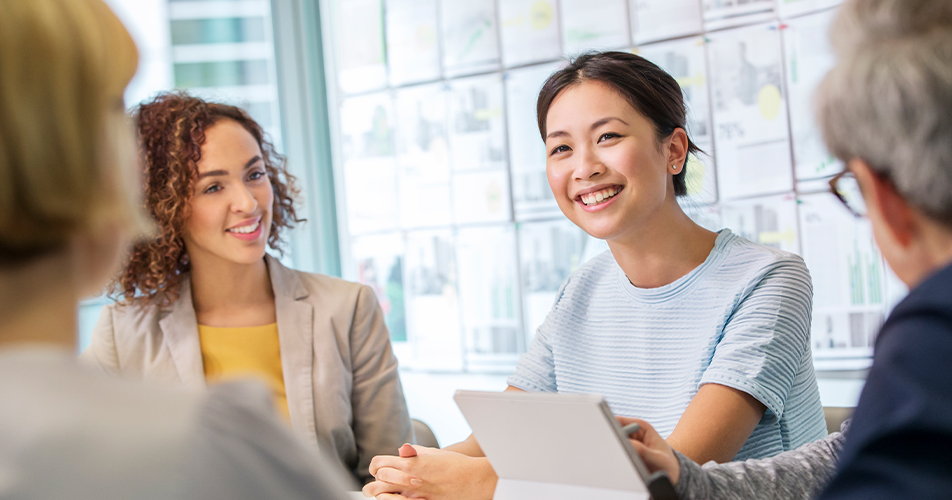