INEOS, Plastic Energy to build pyrolysis-based chemical recycling plant
Mark Victory
22-Apr-2020
LONDON (ICIS)–INEOS and Plastic Energy are to build a new pyrolysis-based chemical recycling plant to come on stream at the end of 2023.
The location of the plant is yet to be decided but is expected to be either at, or close to, one of INEOS’ European cracker sites, a company spokesperson confirmed to ICIS.
The plant will input around 30,000 tonnes/year of mixed, multi-layer, low density polyethylene (LDPE), linear low density polyethylene (LLDPE), high density polyethylene (HDPE) polypropylene (PP) and some polystyrene (PS).
Plastic Energy uses a patented process called Thermal Anaerobic Conversion (TAC), which converts used plastic waste back to TACOIL, which is then used as a feedstock for polymer-chain production.
The waste feedstock is pre-treated to remove contaminants and humidity and to remove plastics other than polyethylene (PE), PP and PS, but processed as a mixed fraction.
The TAC process firstly uses pyrolysis, using temperatures just below 500 degrees Celsius, before cut/collecting the hydrocarbons, distilling and purifying the fractions and upgrading depending on application.
The process has a high yield of, on average, 85% but a major barrier to the growth of chemical recycling has typically been low yields.
INEOS has already completed first trials with TACOIL at its Kohln, Germany, cracker.
“As with many initiatives that INEOS are taking on sustainability, we are choosing to partner with people who are bringing additional supply to the market,” the INEOS spokesperson said.
” It is very important to us to constantly increase amount of plastic which is recycled in line with the INEOS pledge: By 2025, we will incorporate at least 325,000 tonnes/year of recycled material into products [and] offer a range of polyolefin products for packaging applications in Europe containing 50% or more recycled content.”
Other pledges by the chemicals major include to use, on average, 30% recycled content in products destined for PS packaging in Europe and ensure 100% of polymer products can be recycled.
Among European Food Safety Authority (EFSA) requirements for food-grade approval is the stipulation that 95% of the recycled content in a food-grade pellet must have originated from a food-contact source.
For materials such as polyethylene terephthalate (PET), where the major source of post-consumer collection is used plastic bottles, this is relatively easy to ensure.
For materials such as polyolefins, however, where post-consumer collection is comprised of a variety of different types of packaging waste such as domestic and household cleaners, cosmetics as well as food packaging, this represents a significant challenge.
There is no food-grade recycled polypropylene (R-PP) or recycled low density polyethylene (R-LDPE) currently being mechanically recycled from post-consumer waste in Europe.
The UK produces some food-grade recycled high density polyethylene (R-HDPE) because its milk bottles are produced with HDPE.
Most milk bottles in Europe are made from polyethylene terephthalate (PET), and can be easily sorted and separated, but only around 100,000 tonnes/year of milk bottles are collected.
There are also some post-industrial materials that allow for production of food-grade material such as agricultural film or packaging used to transport meat products before they reach consumer.
Nevertheless, these quantities are small.
The attractiveness of chemical recycling is that it allows you to recycle material to produce near identical properties to virgin and allows companies to side-step the traceability requirements for EFSA approval.
This would also circumvent the tensile strength limitations of mechanical plastic recycling.
Plastics cannot typically be endlessly recycled mechanically because every time they are run through the system it weakens the tensile strength of the material until it eventually becomes weak enough that it breaks – the number of cycles this takes differs for each material.
However, there are concerns among mechanical recyclers that, because the majority of chemical recycling process rely on some form of sorting and separating, this will lead to increased competition for higher-quality waste which is already in short supply.
Post-consumer waste bales commonly contain contaminants from materials such as wood, metal and polyvinyl chloride (PVC) that are incompatible with most polyolefin chemical recycling processes.
These materials have to be sorted and separated prior to processing, just as they would in mechanical recycling, except the high heat and pressures used make effective sorting even more critical.
Some processes also require limitations on moisture. Separating and sorting is a costly and highly skilled process, and it remains one of the core challenges across all recycling.
Because of the cost and challenge of sorting and separating, most chemical recyclers are not targeting low quality waste but rather the same waste streams that would typically be used in mechanical recycling.
There are even chemical recycling pilot plants that have been using reprocessed flake material in order to ensure that contamination is avoided.
Front page image source: INEOS
Focus article by Mark Victory
ICIS has launched a new Europe recycled polypropylene (R-PP) price report covering post-consumer and post-industrial bales, flakes and pellets. To subscribe to the new report, or for further information, please contact clientsuccess@icis.com.
Click here to see regulatory targets and a list of chemical and mechanical recyclers on the ICIS Circular Economy topic page.
Global News + ICIS Chemical Business (ICB)
See the full picture, with unlimited access to ICIS chemicals news across all markets and regions, plus ICB, the industry-leading magazine for the chemicals industry.
Contact us
Partnering with ICIS unlocks a vision of a future you can trust and achieve. We leverage our unrivalled network of industry experts to deliver a comprehensive market view based on independent and reliable data, insight and analytics.
Contact us to learn how we can support you as you transact today and plan for tomorrow.
READ MORE
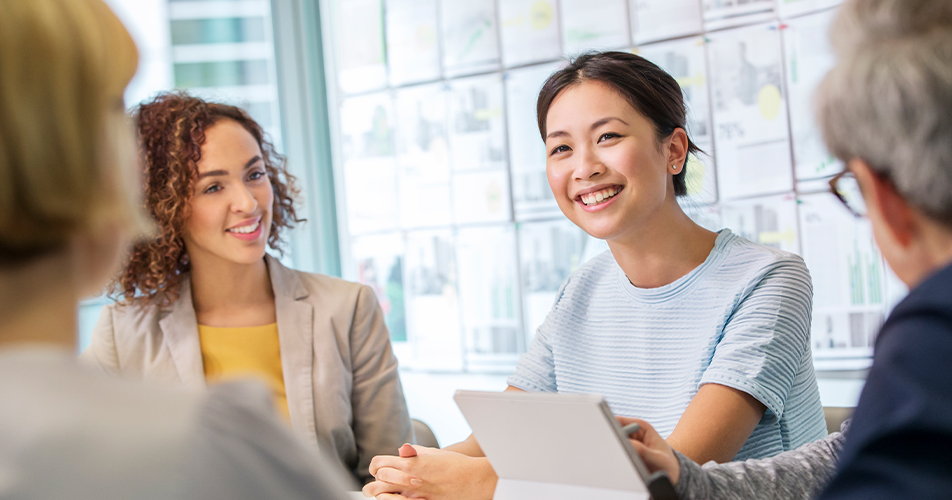