INSIGHT: How the US can achieve high plastic recycling rates
Prashanth Sabbineni
06-Jul-2021
HOUSTON (ICIS)–Recycling to use our planet’s resources more efficiently is an important goal and the role of chemical recycling will be critical in achieving high degrees of plastics circularity.
Chemical recycling is essential to meet ambitious recycling targets, such as the US National Recycling Goal to increase the nation’s recycling rates to 50% by 2030.
Chemical recycling is attractive for recycling plastic wastes that are traditionally non-recyclable to produce virgin-like feedstock. The technology is a sustainable option that significantly reduces landfilling or combusting plastic waste by converting them into new virgin feedstocks that can be used to make new plastics, chemicals, waxes and transportation fuels.
In addition, chemical recycling technologies can use feedstocks that are unsuitable for mechanical recycling to produce high-quality materials equivalent to those produced from virgin resources. These can be used in food contact and pharmaceutical applications. Mechanically recycled plastic can also be used for food packaging, but these uses are subject to food safety certifications. Chemically recycled materials would not require those additional certifications.
Only 12% of plastics were recycled in the US in 2020, while the rest were landfilled, incinerated or exported. Chemical recycling can support higher recycling rates and help brand owners reach their recycled plastic content commitments, while adding an element of sustainability to other fossil-sourced products.
Under status quo, a recycling rate of only 16% in packaging can be achieved with mechanical recycling by 2040, based on studies by ICIS Consulting. A combination of chemical and mechanical recycling can achieve 30% recycled content in plastics packaging by 2030 and 40% recycled content in plastics packaging by 2040. Recognising the essential role chemical recycling plays in creating new markets for used plastics, governmental policies should consider chemical recycling in their frameworks.
PACKAGING WASTE AND
RECYCLING
Plastics play an
important role in modern living. Their
versatility and performance benefits have
enabled wide acceptance of plastics in
packaging, building and construction, consumer
goods, automotive, electrical and electronics,
as well as agriculture.
Packaging comprises one of the largest consuming sectors of plastics, which is where our study is focused. According to the American Chemistry Council (ACC), nearly 42% of the large commodity plastics are used in flexible and rigid packaging that are used for food and non-food applications. These include polyethylene (PE), polypropylene (PP), polyethylene terephthalate (PET), polystyrene (PS), expandable polystyrene (EPS) and polyvinyl chloride (PVC).
Much of the packaging materials end up as plastic waste due to the lack of collection and sorting systems, which reduces end-of-life options for packaging, thus creating a waste management challenge. Recycling is the key that enables plastic to find an end-of-life solution that avoids landfills or incineration.
ICIS Consulting analysed the plastic waste generated by flexible and rigid packaging that consume high-density PE (HDPE), low-density PE/linear low-density PE (LDPE/LLDPE), PP, PET, PS, EPS and PVC and assessed their current and potential recyclability.
ICIS estimates that nearly 32.722m tonnes of plastic waste were generated in the US in 2020. Of the total plastic waste generated, ICIS estimates that only about 19% was collected for recycling. According to the ICIS Recycle Supply Tracker – Mechanical database (which includes PET, PE and PP only), only 12% was mechanically recycled. This leaves 88% of the plastic waste generated that was either not collected or collected but rejected, thus landfilled, incinerated or exported. In both cases, this leaves a significant opportunity for increasing recycle rates.
CURRENT CHALLENGES IN THE RECYCLING
INDUSTRY
ICIS estimates that the
current installed capacity of mechanical
recyclers in the US stands at 6.717m tonnes for
PE, PP, PET, PS, EPS and PVC. As plastics
consumption and subsequently waste generation
grows, higher capacity will be needed to
achieve higher recycling rates. However,
insufficient feedstock due to the lack of a
robust plastic waste collection infrastructure
to provide consistent and low-contaminated
feedstock adds another layer of challenge in
achieving higher recycling rates.
Moreover, not all plastic waste collected can be mechanically recycled due to technical and/or economic limitations. Each time plastics are heated up during processing or mechanical recycling, their quality is reduced by thermal degradation. Measurable loss of physical properties or performance can occur with repeated recycling of higher recycled content levels. That ceiling recycling rate will vary based on the polymer, the temperatures at which it was processed/recycled and the requirements of the end-use application.
While large, clean, homogenous plastic items can be cost-effective to recycle, small, mixed and contaminated plastic articles are not. Although collected, recyclers may reject plastic waste due to contamination with food, hazardous materials, cross-contamination with other polymers and a range of other reasons. In addition, many types of plastic packaging are multilayered, with each layer adding specific performance criteria, like an oxygen barrier that preserves freshness. This layered or mixed material is not practical for mechanical recycling, but can be chemically recycled. Chemical recycling enables the processing of contaminated and mixed plastic waste, which would otherwise end up in landfills or incinerators.
THE ROLE OF CHEMICAL RECYCLING IN
ACHIEVING INDUSTRY
TARGETS
Considering the
increasing consumer demand for recycled
plastics, ICIS Consulting further analysed the
current status of mechanical recycling and the
forecast mechanically and chemically recycled
volumes needed to meet demand under different
hypothetical national minimum recycled content
scenarios. Data presented represents packaging
only and pertains to HDPE, LDPE/LLDPE, PP, PET,
PS, EPS and PVC.
In Scenario 1, at status quo, ICIS grouped packaging demand into flexible and rigid categories and forecast the growth of these streams under current market drivers and presented it in Table 1 below.
Under current market drivers for recycled content in packaging, the increase in recycling is largely dependent on the growth of recycling capacity as driven by brand owners’ demand. The current installed mechanical recycling capacity in the US stands at 6.717m tonnes against 16.899m tonnes consumed in packaging in 2020, leaving a wide opportunity for recycling growth. In this scenario, the plastics recycling rate is expected to reach a modest 16% in 2040.
Scenario 1 | 2020 | 2025 | 2030 | 2035 | 2040 |
Rigid plastic non-food/pharma packaging containers | 2,697 | 2,991 | 3,233 | 3,431 | 3,612 |
Food/pharma rigid packaging and containers | 6,801 | 7,693 | 8,287 | 8,748 | 9,200 |
Plastic carryout bags, non-food contact packaging | 4,878 | 5,392 | 5,813 | 6,163 | 6,484 |
Food/pharma plastic film and flexible packaging | 2,524 | 2,709 | 2,853 | 2,960 | 3,072 |
Total Packaging Demand | 16,899 | 18,785 | 20,186 | 21,302 | 22,368 |
Packaging Market Growth, CAGR | – | 2.10% | 1.40% | 1.10% | 1.00% |
Polymers Total Demand (all end-uses) | 28,769 | 32,184 | 34,625 | 36,710 | 38,733 |
Total Recyclate (all end-uses) Output-ICIS estimate | 3,567 | 4,102 | 4,657 | 5,301 | 6,077 |
Recyclate Share of Total Demand | 12% | 13% | 13% | 14% | 16% |
Table 1: Forecast of Plastics Recyclate in
Packaging – Scenario 1. Data in thousands of
tonnes.
Source: ICIS Supply & Demand Database,
ICIS Recycle Supply Tracker – Mechanical
The mechanical recyclate output presented in the Table 1 may be used for other end uses as well as packaging.
Several brand owners have committed to using 25-30% minimum recycled content in their packaging by 2025 and California has mandated manufacturers to include an annual average of 25% of post-consumer recycled plastic (PCR) in beverage containers by 2025. A few other states have similar bills underway. This forms the basis of Scenario 2. It assumes a nationwide requirement for all packaging as opposed to 50 different state requirements, starting with 25% of recycled content by 2025 and increasing by 5% every five years to 2040. To achieve this goal, ICIS Consulting has determined that chemical recycling will be needed to meet the demand.
Scenario 2 | ||||
PACKAGING MARKET | 2025 | 2030 | 2035 | 2040 |
Rigid plastic non-food/pharma packaging containers | 2,991 | 3,233 | 3,431 | 3,612 |
Minimum recycle content required | 25% | 30% | 35% | 40% |
Minimum recycled resin required | 748 | 970 | 1,201 | 1,445 |
Food/pharma rigid packaging and containers | 7,693 | 8,287 | 8,748 | 9,200 |
Minimum recycle content required | 25% | 30% | 35% | 40% |
Minimum recycled resin required | 1,923 | 2,486 | 3,062 | 3,680 |
Plastic carryout bags, non-food contact packaging | 5,392 | 5,813 | 6,163 | 6,484 |
Minimum recycle content required | 25% | 30% | 35% | 40% |
Minimum recycled resin required | 1,348 | 1,744 | 2,157 | 2,594 |
Food/pharma plastic film and flexible packaging | 2,709 | 2,853 | 2,960 | 3,072 |
Minimum recycle content required | 25% | 30% | 35% | 40% |
Minimum recycled resin required | 677 | 856 | 1,036 | 1,229 |
Minimum required recycled resin in packaging | 4,696 | 6,056 | 7,456 | 8,947 |
Forecast of mechanical recyclate production | 4,102 | 4,657 | 5,301 | 6,077 |
Chemical recycling production needed to meet minimum content | 594 | 1,399 | 2,155 | 2,870 |
MECHANICAL RECYCLING SHARE IN PACKAGING | 87% | 77% | 71% | 68% |
CHEMICAL RECYCLING SHARE IN PACKAGING | 13% | 23% | 29% | 32% |
Table 2: Forecast of Plastics Recyclate in
Packaging – Scenario 2. Data in thousands of
tonnes.
Source: ICIS Supply & Demand
Database
The mechanical recyclate production presented in the Table 2 assumes all of it is used for packaging. However, recycled material may be used for all end uses, indicating higher mechanical recyclate production and capacity are needed to meet the minimum recycled content requirement. Chemical recycling can help close the capacity deficit to meet the expected demand for recycled plastics.
In the US, the federal definition of recycling currently does not consider chemical recycling, although an increasing number of individual states consider chemically recycled materials as recycled. As the data under Scenario 2 suggests, mechanical recycling production will not be sufficient to fulfil the requirement and chemical recycling will be needed to meet the minimum required recycled resin content in packaging. This presents the need to include chemical recycling under recycling.
Chemical recycling has the potential to contribute to a robust circular economy by supporting higher plastic recycling rates, reducing strain on the use of fossil fuels. While there are studies underway to determine the impact of chemical recycling on carbon emissions, chemical recycling does emit less carbon dioxide (CO2) than incineration. Chemical recycling is not a fully mature industry and will likely see improvements in the near future. Major investments are needed in building production-scale chemical recycling plants. The success of the technology depends on improving collection and sorting mechanisms. It is not guaranteed that chemical recycling will provide the solution to meeting recycling targets by 2025. Uncertainties exist around the timeframe for scale, the quality of waste inputs, the costs of chemically recycled products and the environmental footprint. Nevertheless, chemical recycling can complement mechanical recycling to achieve large-scale plastics circularity in the longer term.
By Prashanth Sabbineni, James Ray and Paula Leardini
Global News + ICIS Chemical Business (ICB)
See the full picture, with unlimited access to ICIS chemicals news across all markets and regions, plus ICB, the industry-leading magazine for the chemicals industry.
Contact us
Partnering with ICIS unlocks a vision of a future you can trust and achieve. We leverage our unrivalled network of industry experts to deliver a comprehensive market view based on independent and reliable data, insight and analytics.
Contact us to learn how we can support you as you transact today and plan for tomorrow.
READ MORE
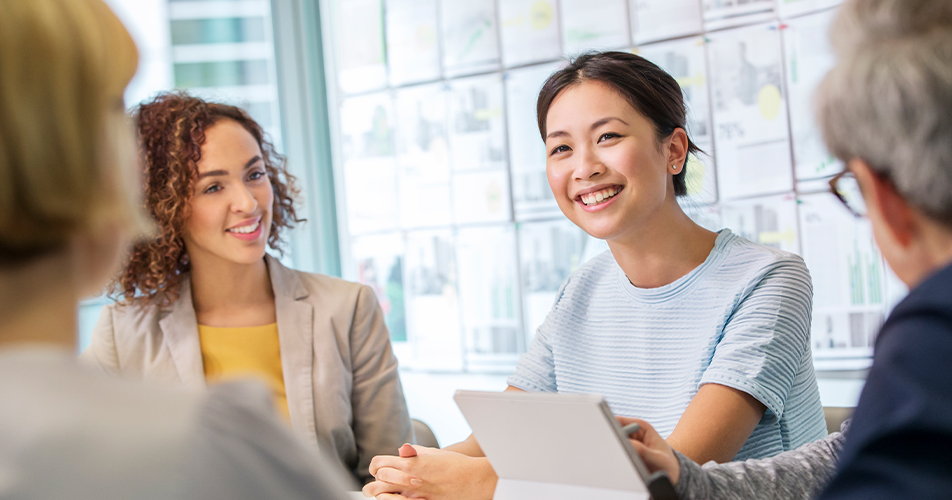