AFPM ’21: Supply chain strains, logistics woes to persist into 2022
Adam Yanelli
16-Oct-2021
HOUSTON (ICIS)–The coronavirus pandemic disrupted every aspect of life, including the supply chains that have been built up over time to consistently deliver goods and raw materials to various parts of the world.
Heading into this year’s International Petrochemical Conference (IPC), those supply chains have been pressured like never before and at every leg of the journey amid surging demand as economies reopened from COVID-19 lockdown measures and consumers rushed to spend stimulus money or savings on goods, many originating from China and east Asia.
This crush of demand created new headwinds as ports saw record levels of congestion, and also revealed existing strains such as the shortage of truck drivers and unwillingness of railroads to use policies like reciprocal shipping.
Chemical supply chains had been resilient, but late-season hurricanes in 2020 and winter storm Uri in February forced the shutdown of much chemical production in the US Gulf, which crimped supply and added additional stress to supply chains.
The strained supply chains have resulted in longer lead times and even possibly to the cancellation of some orders as importers during the peak shipping season ahead of the Christmas holiday come to the realization that their goods are unlikely to arrive in time.
Supply-chain strains also contributed to the International Monetary Fund (IMF) slightly lowering its 2021 global GDP forecast.
“Pandemic outbreaks in critical links of global supply chains have resulted in longer-than-expected supply disruptions, further feeding inflation in many countries,” the IMF said on 12 October in its World Economic Outlook.
SHIPPING
While most chemicals are liquids and are
shipped in tankers, plastics like polyethylene
(PE) and polypropylene (PP) are shipped in
containers and are having to compete with
traditional imported goods.
This has led to a spike in rates for shipping containers, primarily out of China and east Asia.
Containers that used to cost around $6,000 jumped to more than $22,000. Levels have pulled back to below $20,000 over the past three weeks but remain elevated.
Because of the strong demand in the US, importers have paid the higher prices, leading to record levels of congestion at the nation’s largest container ports.
For example, as of 13 October, there were 86 container ships in port at the ports of Long Beach and Los Angeles, according to the Marine Exchange of Southern California (MESC).
MESC defines total vessels in port as the sum of vessels at anchor, in a drift area, and at berth.
That is down from 97 in anchor on 21 September and down from the record 100 set on 19 September.
Jonathan Gold, vice president of supply chain and customs policy for the National Retail Federation, said a survey of its members indicated that most are seeing disruptions in their supply chains.
He added that the port congestion issues have expanded from the major ports as importers look for ways to speed up the delivery of their goods.
Gold offered some advice on how importers can mitigate the current situation.
“We are in the thick of it now, and hopefully people have been planning ahead with some type of mitigation to get product here,” he said during a webinar.
First, importers must be in regular communication with their overseas providers and vendors to make sure they are clear on what its procedures are.
Second, he said smaller and medium-sized companies could partner up with competitors to increase their bargaining power based on higher volumes.
And last, he suggested reaching out to the ports and terminals to see if there is anything that a company can do to help speed up the process.
PORT CONGESTION
The ports of Los Angeles and Long Beach
recently enacted new policies designed to help
improve the situation.
The Port of Los Angeles agreed to move to 24 hours, seven days a week operation after meeting with US President Joe Biden and members of the administration.
The Port of Long Beach made the change last month.
The ports are the two largest ports in the nation, first and second respectively, and combined are the ninth-largest port complex in the world.
Robert Khachatryan, founder and COO of shipping forwarder Freight Right Global Logistics, said he has yet to see any difference.
“I do not think it has moved the needle at all,” he said. “Yes, they allow truckers to go in at night and pick up containers, but they are not operating with any more capacity within the port – so the container works, the vessel works aren’t really expanding.”
He also noted that just because a driver could technically pick up a container at night, there are very few companies that will accept deliveries after hours.
“So even if they pull these containers, there is nowhere to take them,” he said. “It is not an effective change.”
TRUCKING
The trucking industry has been dealing with a
shortage of drivers for years, but it
intensified during the pandemic as truck
driving schools were unable to operate during
the lockdowns.
Bob Costello, chief economist and senior vice president at the American Trucking Associations (ATA), told delegates at the Independent Lubricant Manufacturers Association (ILMA) annual meeting this week in Phoenix, Arizona, that availability of both trucks and drivers are ongoing issues.
“This is a challenge like we’ve never seen before,” he said, pointing to year-on-year strength in three main drivers of truck freight: Retail sales (up 20.6%), single-family housing starts (up 23.2%) and manufacturing output (up 7.6%).
Trucking lines are reducing truck counts because of the inability to add drivers, selling parked trucks and independent contractors are going to the spot market, Costello said.
Costello said the driver shortage is not new, but is getting worse and driven by demographics and lifestyle.
The average age of long-haul truck drivers is well over 50 and predominantly male, despite females accounting for 47% of the US workforce. New trainees average 35 years old, so the age issue is not improving.
RAIL
In the US, chemical railcar loadings represent
about 20% of chemical transportation by
tonnage, with trucks, barges and pipelines
carrying the rest.
Also, about 30-35% of all containers that come into the ports of Los Angeles and Long Beach are loaded directly onto rail cars.
Rail companies have been working to improve delivery times and availability.
In July, Union Pacific Railroad temporarily suspended eastbound movement from West Coast port terminals to Chicago for seven days in an effort to ease inland congestion as rail shipments to and from the ports had risen and are near record highs.
UP said in a monthly update on 24 September that it has seen improvement is some of the metrics it uses to track efficiency.
Car velocity improved by 11% and is above 200 miles/day for the third consecutive week, and train velocity has improved by 9%. Car dwell, or the amount of time a railcar is sitting unused, fell by 7%.
In July, the Rail Customer Coalition (RCC) urged the members of the US Surface Transportation Board (STB) to take action to improve rail service and reduce costs for customers.
The RCC represents a broad range of manufacturing, agricultural, and energy industries that depend on the railroads to deliver reliable and affordable service, including the Renewable Fuels Association, American Petroleum Institute, the American Chemistry Council and the American Fuel & Petrochemical Manufacturers.
The group would like to see the railroads take up a proposal that the STB made in 2016 for reciprocal switching, which would allow a shipper to gain access to another railroad under certain circumstances.
Reciprocal switching refers to the situation in which a railroad that has physical access to a specific shipper facility switches rail traffic to the facility for another railroad that does not have physical access.
The second railroad pays compensation to the railroad that has physical access, typically in the form of a per car switching charge.
As a result of the arrangement, the shipper facility gains access to an additional railroad.
WHEN WILL IT END?
Despite the best efforts of all involved, the
supply-chain constraints are unlikely to go
away anytime soon.
The driver shortage will be a lingering issue as it was prior to the pandemic.
And the ocean freight strains are also unlikely to ease.
“This is not going away tomorrow, not the next quarter,” said Eytan Buchman, chief marketing officer at online freight shipping marketplace and platform provider Freightos. “I think the pressure on shipping is going to exist until at least the middle of next year.”
Hosted by the American Fuel & Petrochemical Manufacturers (AFPM), the IPC takes place on 17-19 October in San Antonio, Texas.
Focus article by Adam Yanelli
(Thumbnail image shows a container ship. Photo by Seth Wenig/AP/Shutterstock)
Global News + ICIS Chemical Business (ICB)
See the full picture, with unlimited access to ICIS chemicals news across all markets and regions, plus ICB, the industry-leading magazine for the chemicals industry.
Contact us
Partnering with ICIS unlocks a vision of a future you can trust and achieve. We leverage our unrivalled network of industry experts to deliver a comprehensive market view based on independent and reliable data, insight and analytics.
Contact us to learn how we can support you as you transact today and plan for tomorrow.
READ MORE
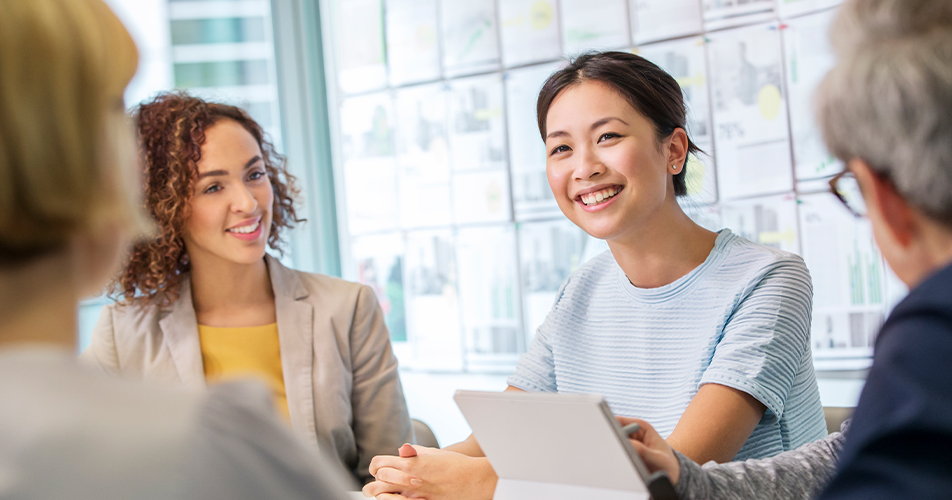